NEWS
2024.02.02
What's CellQualia?
"CellQualia" is the brand name for the regenerative medicine products of Sinfonia Technology.CellQualia is a word we coined by combining the word "Cell" with the word "Qualia", which reminds us of quality.
The word "qualia" itself is defined as "a distinctive and vivid texture associated with sensory experience" (Kojien), but the word itself is derived from the Latin noun for "quality", "qualitas The origin of this word is the Latin noun "qualitas", which means "quality", and the brand name expresses our desire to focus on the quality of our cells.
With the CellQualia brand, we will continue to provide solutions that contribute to the production of high quality cells.
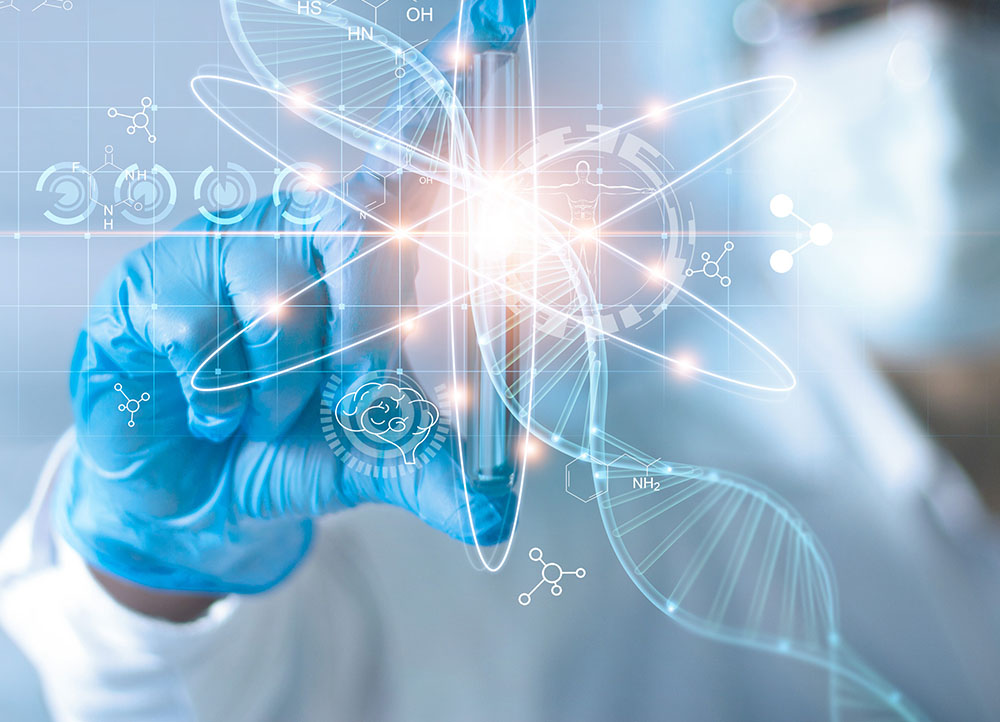
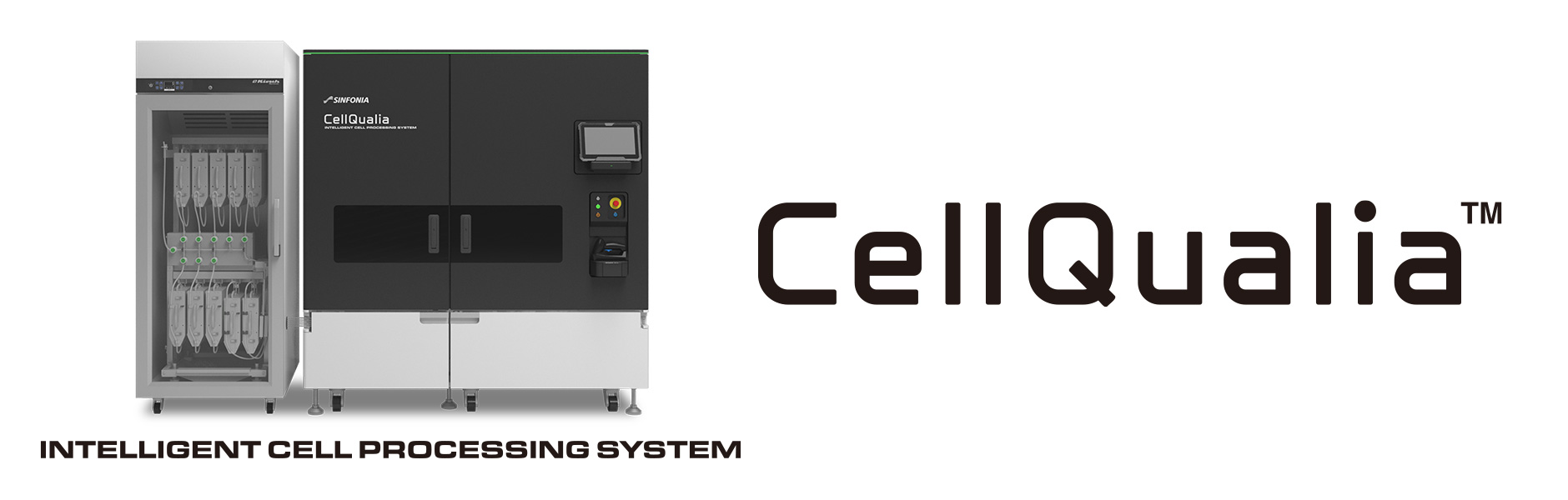
CONCEPT
Bringing Manual Cell Culture to Automated Manufacturing, to deliver a higher level of quality control
What's QbD?
In regular cell processing, the quality of raw materials (cells) varies and status of culture changes from moment to moment with conditions and time.
The idea of Quality by Design (QbD) is to analyze such fluctuations, find out the relationship with the quality of the final product, and then set allowable range of fluctuations for successful manufacturing.
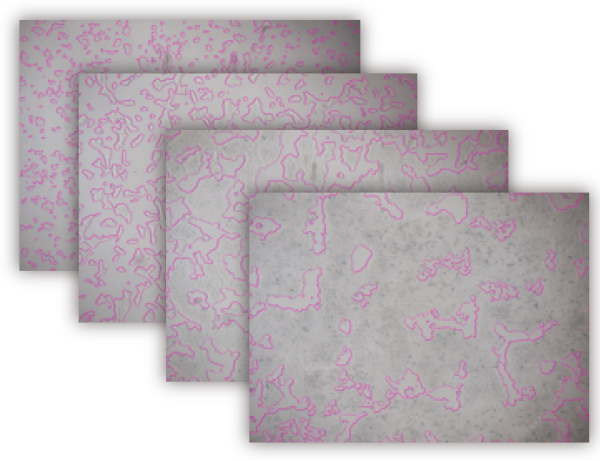
Realization of cell culture production based on QbD
Intelligent Cell Processing System is equipped with Process Analytical Technology (PAT) to monitor culture status in real time, and stabilizes process by automation, these enable us to manufacture cell products based on QbD consept.
Joint development with the Foundation for Biomedical Research and Innovation(FBRI) at Kobe.
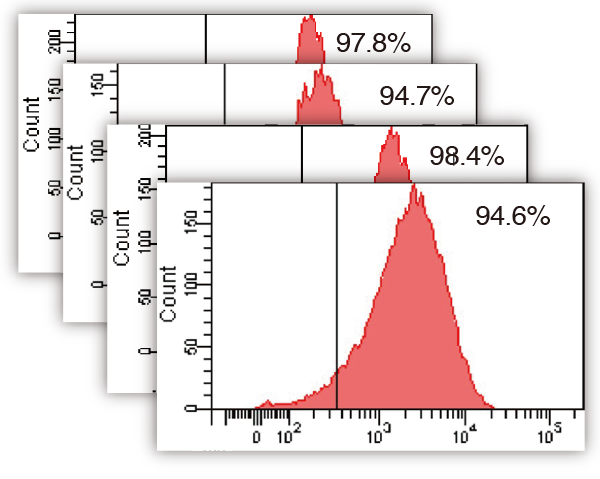
Features
Automated cell culture from sowing to passaging to harvesting
Automated sowing, process monitoring, medium change, passaging and harvesting.
Fully closed system
The aseptic connection between the disposable kit, consisting of bags and tubes, and the culture vessel provides a completely closed system. Eliminates the possibility of contamination. Can be used in Grade C areas.
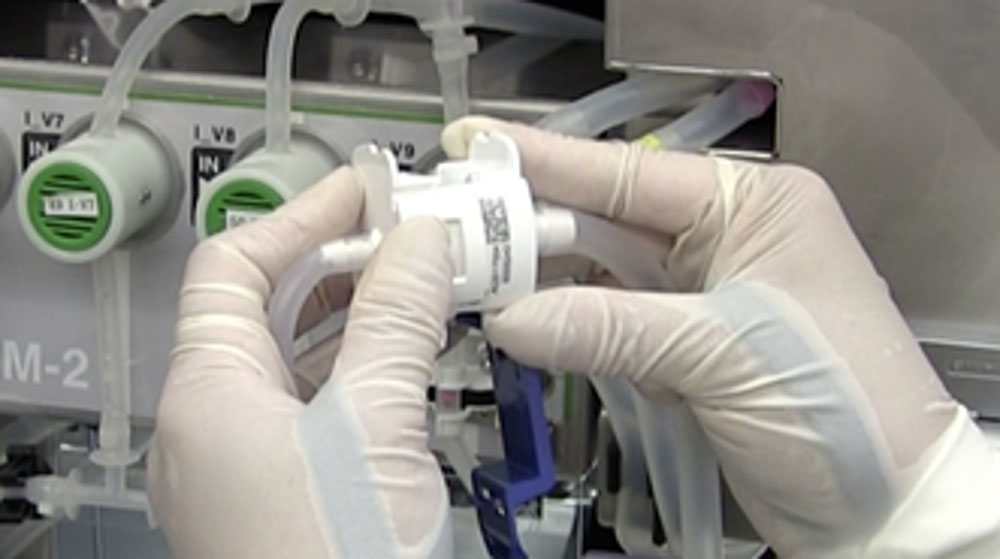
Automatic passaging function
Two standard multilayer culture vessels (Corning CellSTACK) can be set up simultaneously.
First: 1-layer or 2-layer flask (min. 636 cm2) Second: 5-layer or 10-layer flask (max. 6360 cm2)
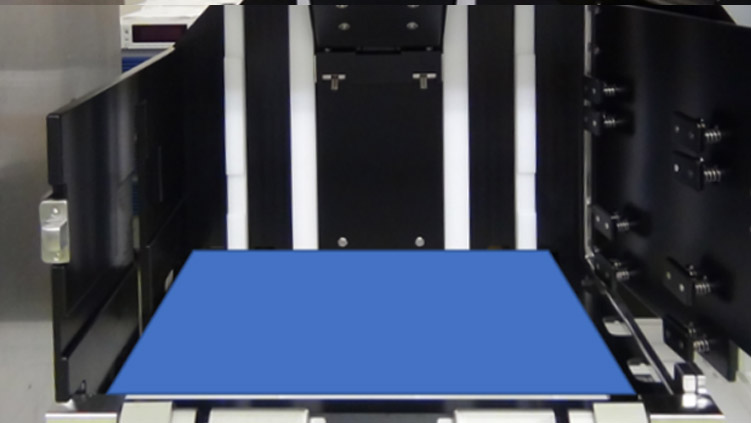
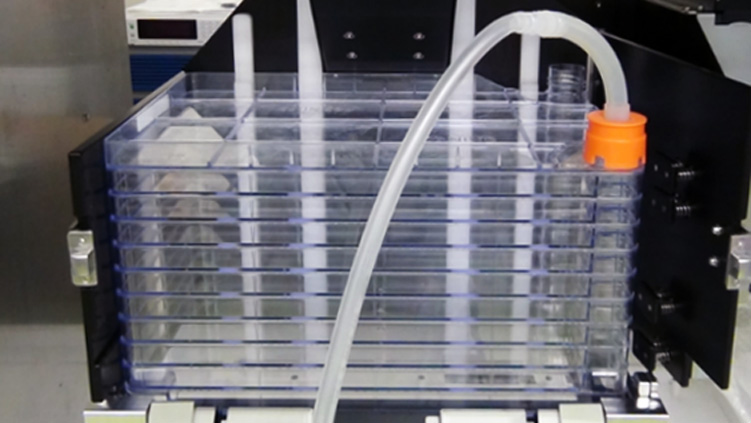
After passaging, the first culture vessel can be manually replaced by a third vessel for further passaging.
Real-time imaging
The CMOS camera automatically stores image data of cell morphology and growth.
Inline process analysis technology
Automatic analysis of glucose, lactic acid and pH by medium analysis sensor.
Off-line analysis with automatic sampling
Off-line medium/biomarker analysis is possible by automatic extraction into a sampling bag.
Kynurenine and 2aminoadipic acid, which are considered to be excellent biomarkers for the pluripotency status of ES and iPS cells, are available for analysis on the LC/MS system by sampling.
Connectivity with higher-level production management systems (in preparation)
Fully integrated workflow management software from material management to outgoing product inventory management.
Interface to higher-level systems for production execution and control.
CellQualia-Intelligent Cell Processing System- is a
GMP-compliant production of iPS/ES cells and MSCs.
Culture Data
iPSC
Cell growth monitoring by imaging (iPS cells)
Cellular images were taken at each day by CMOS camera at the bottom of multi-layer flask. The edge of iPS cell colony (pink lines) was drawn by image analysis system and growth curve was predicted by confluency.
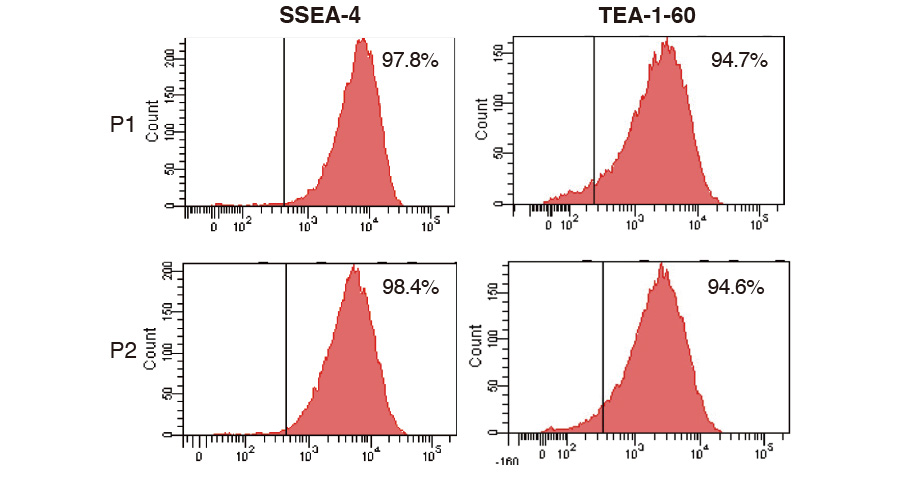
Influence of automated expansion (iPS cells)
MSC
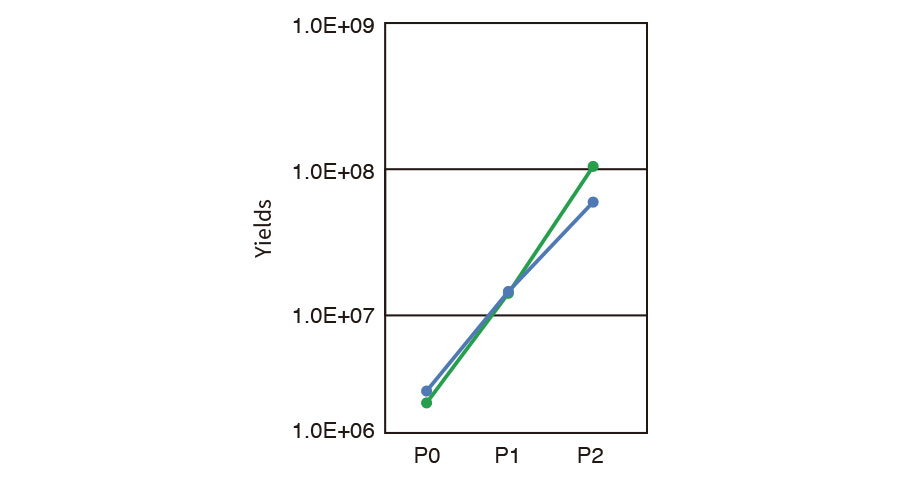
Passaging and harvesting (MSC)
Pre-cultured MSCs were seeded into CellSTACK® (1 layer, Corning) to be 2.0E+6 cells (P0) and cultivated for 3 days. The cells were passaged to larger CellSTACK® (5 layer) in an automated manner and aliquot of cells was sampled and counted (P1). At 3 days after sub-cultivation, all of the cells were harvested by ICP and counted to estimate yield at the final step (P2).
Quality of product (MSC)
MSCs were expanded with ICP, harvested, dispensed in vials and cryopreserved. The cells thawed and re-cultivated were confirmed to express MSC marker at high level (each graph) and grow on plastic surface (photo); these results showed that MSC keeps their characteristics after expansion with ICP.
System Configuration
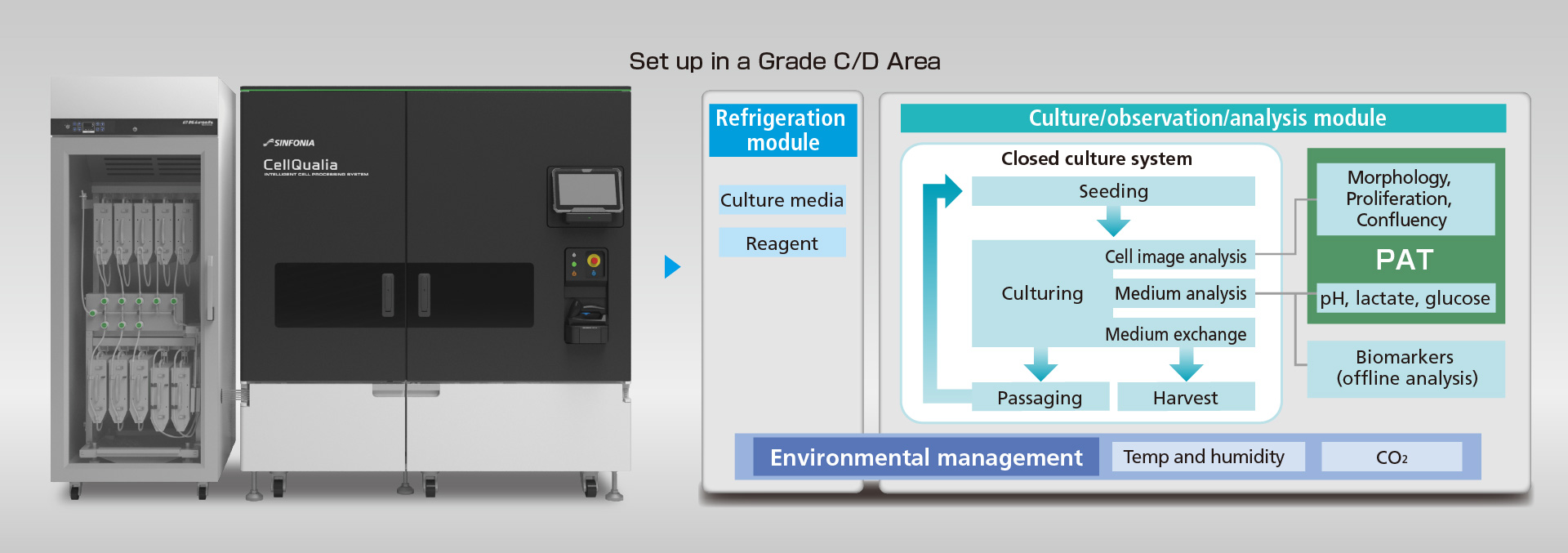
Completely closed system to eliminate the possibility of contamination, operating in Grade C areas
VIDEO
ADVANTAGE
We have developed an automatic cell culture system based on the idea of Quality by Design proposed by Dr.Shin Kawamata.
Joint development with Dr.Shin Kawamata, Director of Foundation for Biomedical Research and Innovation at Kobe(FBRI).
MORE DETAIL
Cell types | Adherent cells (iPS cells, MSC) |
---|---|
Function (culture) |
Seeding, medium exchange, passage, harvest |
Function (analysis) |
Image observation, culture media analysis |
Culture container | Multi-layered container |
Culture surface | Max. 18,000 cm2 |
Shape analysis | CMOS camera |
Culture media analysis |
Inline: lactic acid, glucose, pH Offline: Biomarkers (2-aminoadipic acid, kynurenine) Measured with another device |
Power consumption | Typical 2.0kW Max 3.7kW (at 200V) Typical 2.2kW Max 3.8kW (at 240V) |
---|---|
Power supply | AC200V-AC240V 1φ 50Hz/60Hz |
UPS | Optional (MAX 3,000VA) |
Ambient environment |
Temp:18-25℃T Humidity:75% or less (no condensation) Cleanliness: Grade C |
Outer dimensions | W 2,670× D 931× H 1,995mm (no protruding parts) |
Weight | Approx. 1,300kg |
Air supply | CO2, clean-dry air (both should be 0.3-0.5MPaG) |
Standard | CE,UKCA,UL |
Disposable parts
・Disposable closed-system culture kit ・Culture vessels
SOLUTION LAB
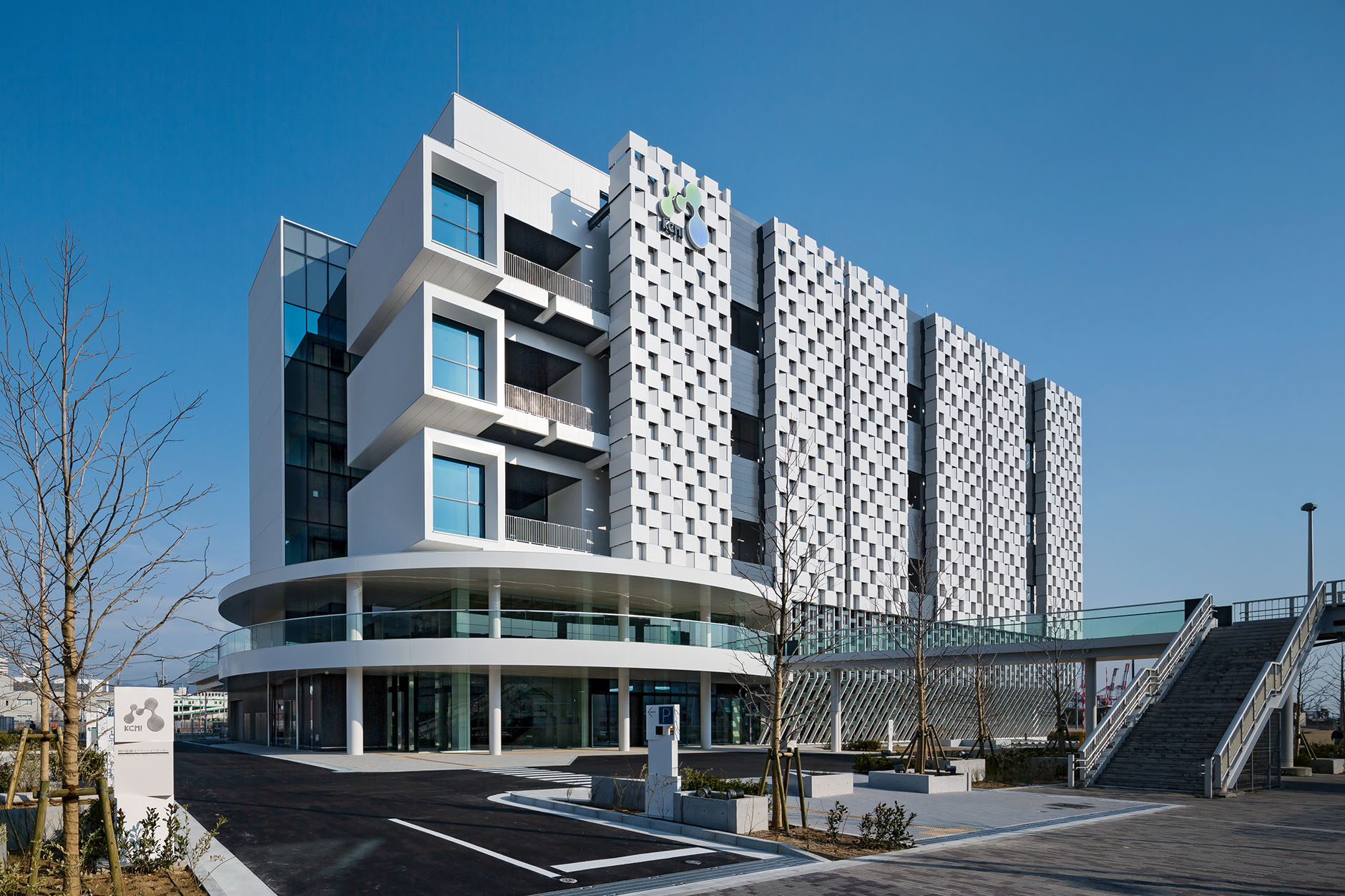
Kobe Center for Medical Innovation KCMI
SINFONIA TECHNOLOGY's Solution Lab is a base for cell production-related customer services, such as user training, demo / paid runs and contract manufacturing, by our resident staff. The facility is a compact CPC at the Grade C level, which is a recommended environment for CellQualiaTM Intelligent Cell Processing System installation. We believe that an efficient use of our Solution Lab can accelerated the realization of QbD in your cell manufacturing.
Sinfonia Technology has acquired a patent license from iPS Academia Japan, Inc. for instrument demonstration and user training use of prescribed iPS cells. Please contact us in advance if you want to use the other iPS cells.
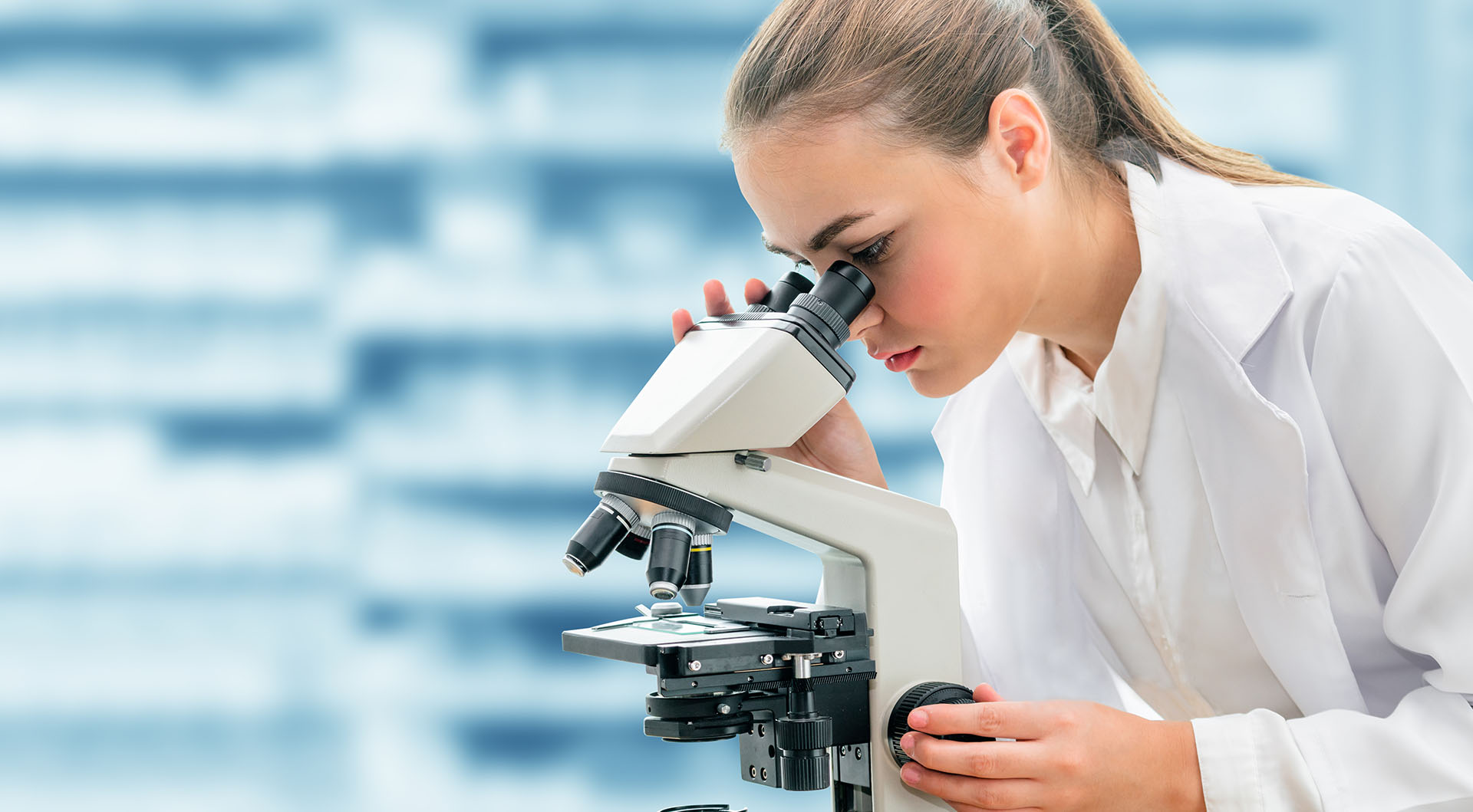
About
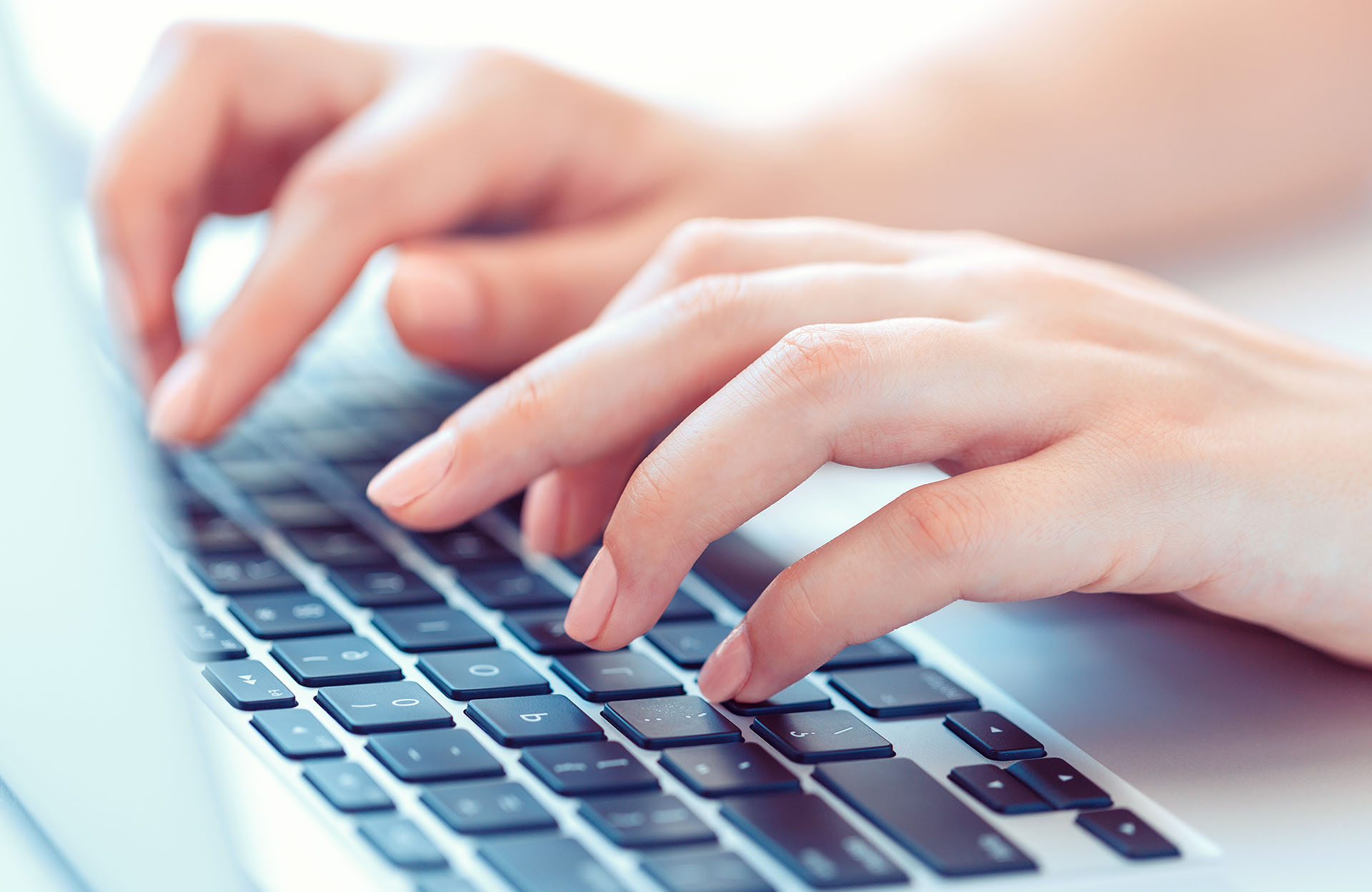